
#Automatic feeder fish manual#
One worker would cost 1.6 USD/h if we used manual feeding and put in a lot of effort and went to the tank farm twice a day. It is claimed that the cost of the automatic feeder with one operator can be ignored when measuring cost because of the small use of electric power of a few watts and the cost of about 1.7 USD/h for the first feed for half day and on their day, they did not require a worker for two feeds, implying that there are three rations for two days.
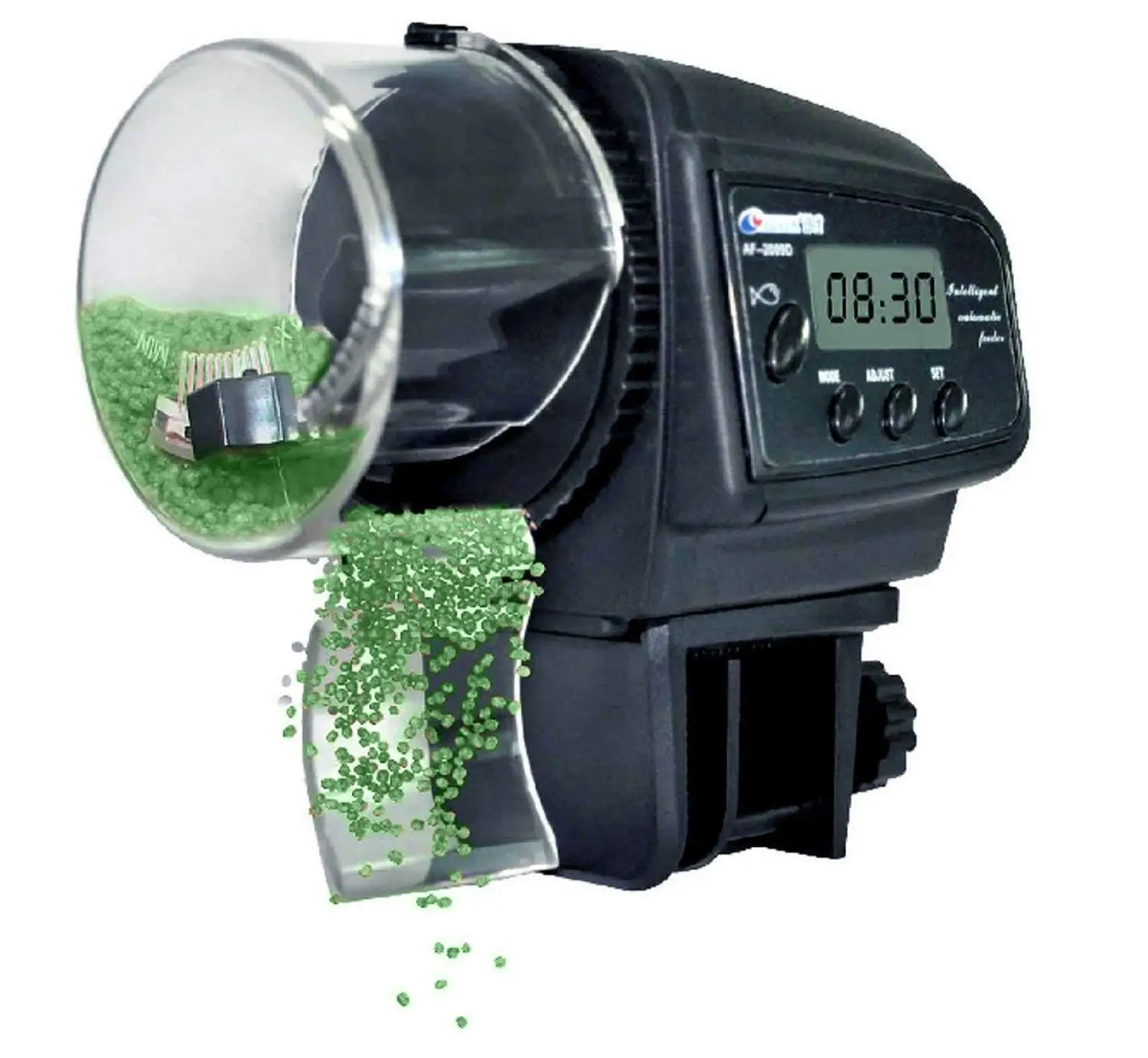
This system does not perform well with spread food or intensive feeding since it uses an infrared photoelectric sensor to start and stop feeding based on the gathering behavior under the feeder. These findings show that in the last phases of cage-raising Nile tilapia, a higher feeding rate combined with efficient feed management can be used without sacrificing end fish productive quality. There was no difference in the viscerosomatic index, indicating that the ultimate carcass quality had not changed. The fish treated with 4% of their live weight at 30 min intervals between meals had the greatest average weight of 683.73 g. The mean values for dissolved oxygen, pH, and temperature for the experiment were 3.20 mg/L, 8.03, and 25.43 ☌, respectively. In one pond, eighteen 1 m 3 net cages with automatic feeders were spread. The basic information derived from the development of automatic feeder feeding strategies, tilapia weighing 185 g were fed 48 meals a day at 22 or 30 min intervals, with feeding rates of 2, 3, and 4% of live weight, in a study conducted from September to December. Per tank, 198 fish (60 fish per m 3) were stocked. To keep the water volume at 3.2 m 3, the water level was kept at 80 cm deep. Each rearing tank measured 2.9 m in length, 1.4 m in width, and 1 m in depth. A simple human-powered fish feeding system was built in the study to solve the feeding problem in a freshwater aquaculture on a budget. Developing-country fish farmers find manual feeding to be more cost-effective than costly mechanized feeding. Increasing the number of daily feedings from two to six can allow for a higher daily feeding rate, which translates into higher growth and production. There are several automatic feeders which have been developed to fulfil certain objectives and requirements. A self-feeder’s response times vary from 3 to 15 s and 1 min. When the temperature is high, metabolic processes increase, therefore, a high food demand is present on the other hand, when the temperature is low, food demand decreases too. The cost of aquaculture feeds can account for from 30 to 60% of total operating costs in aquaculture production. The cost of raw material, as well as the equipment used in the production and processing of the feed, contribute to the high cost of aquaculture feed. Furthermore, due to high feed costs and the possible negative effects of waste feed on water quality, wastage must be reduced. Since fish farmers must ensure that feeding regimes, feeding rates, ration sizes, and the period over which they are dispensed are adjusted to optimize consumption, growth, and conversion efficiencies, the expression of feeding behavior and the satiation time are both important. In intensive fish culture systems, fish may be fed as many as five times a day to maximize growth at optimum temperatures. Generally, growth and feed conversion increase with feeding frequency. Feeding frequency is dependent on labor availability, farm size, as well as fish species and sizes. Furthermore, the feeder used very little electricity and saved time, cost, labor, energy, and pellets.įeeding fish is labor-intensive and expensive. The results showed that the optimal speed for the automatic feeder was 14 rpm with a height of 70 cm, resulting in a distribution width of 26.6 cm and a high automatic feeder efficiency of 99.9%. Three pellet sizes, three rotation speeds, and three feeder heights from the water’s surface were used to test the automatic feeder’s efficiency. The dispensed feed operated by a DC motor located underneath the pellet hopper and the feed material was discharged into the tank through a gate in the bottom of the feeder.
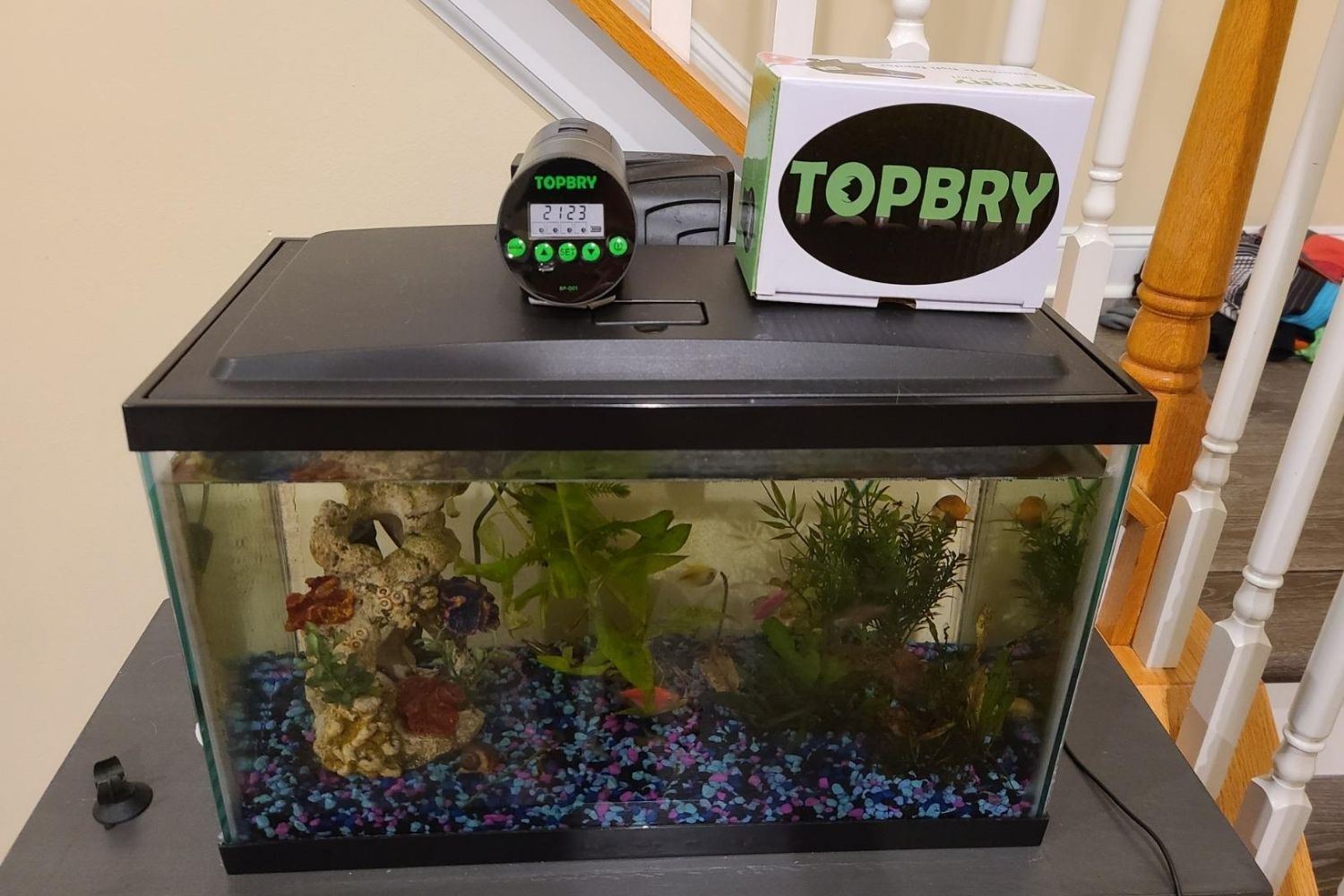
The performance of the prototype was studied after it was designed and installed.
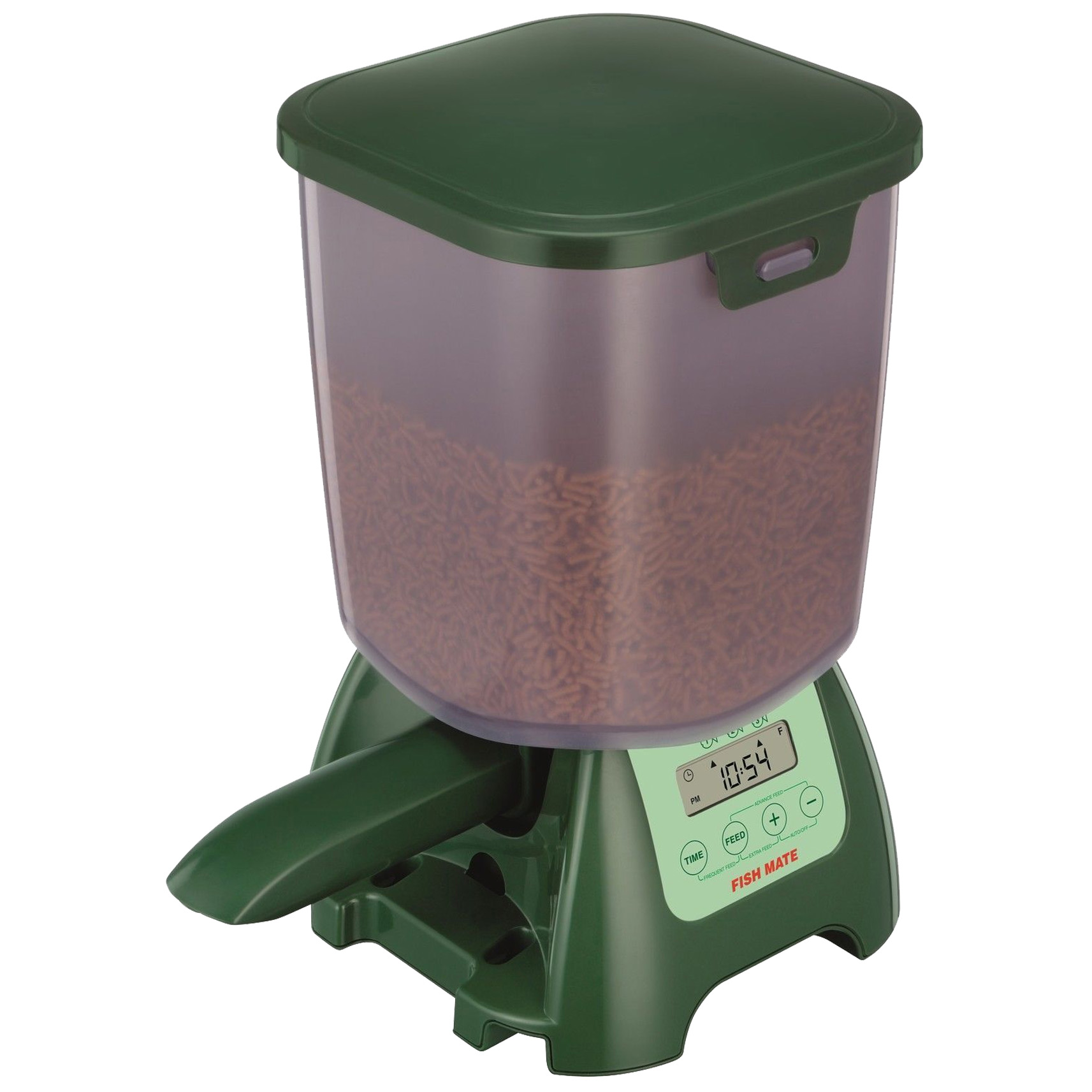
Developing-country fish farmers use manual feeding to be more cost-effective than with costly mechanized feeding, so this research aimed to design and construct an automatic fish feeder prototype to feed tilapia in a recirculation aquaculture system’s tank.
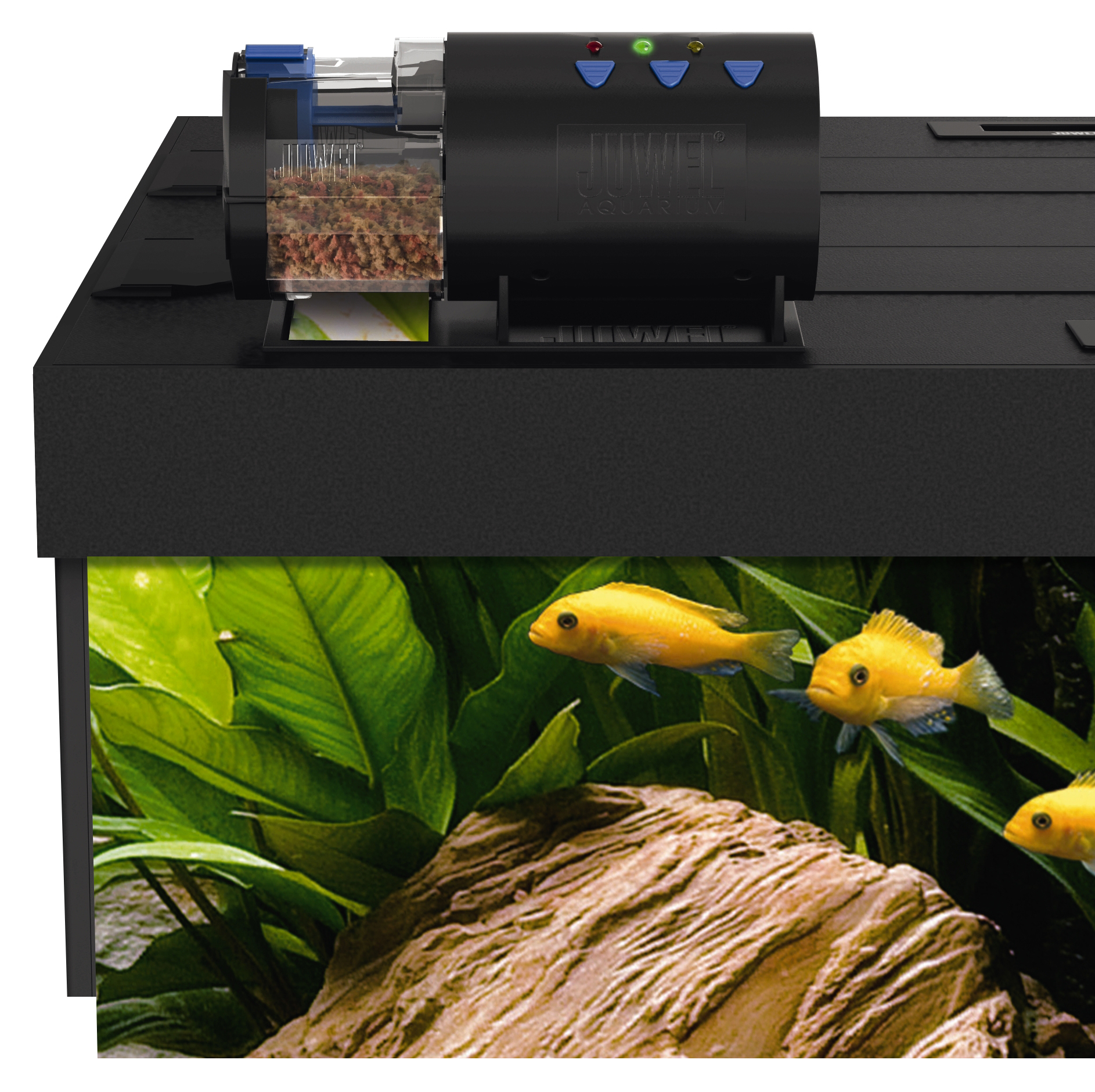
It is better to find new a automatic feeder saving pellets from crushing and cohesion without hitting pellets during feeding at a predetermined interval of time and an accurate amount of food with a larger surface area covered by pellets. The conventional methods of supplying feed to tilapia tanks are ineffective.
